Machine Condition Monitoring: A Detailed Guide & Case Study
An average large plant loses 25 hours a month to unplanned downtime, according to The True Cost of Downtime report by Siemens. It’s more than a full day’s production. Machine breakdowns cost billions in lost revenue and repairs for manufacturers.
What does the IIoT (Industrial Internet of Things) have to offer? Let’s take a look at machine condition monitoring. It’s a proactive approach that relies on real-time sensor data to predict faults, including bearing issues, excess heat, and gear tooth surface wear.
In this article, we'll explore the efficiency of machine condition monitoring, compare it to traditional methods, and delve into its operational stages. Also, we will introduce our machine condition monitoring solution in collaboration with SIA Connect.
What’s machine condition monitoring?
Machine condition monitoring, also known as condition-based monitoring, is a maintenance approach that anticipates machine health and safety. It relies on real-time machine sensor data to predict potential issues.
Condition monitoring techniques extend across diverse equipment types, including rotating machinery, auxiliary systems, and components like compressors, pumps, motors, and presses. This comprehensive approach considers various factors, including efficiency, wear and tear, performance indicators, usage statistics, and maintenance records.
Which faults can be identified through machine condition monitoring?
- Bearing issues
- Excess heat
- Shaft unbalance
- Gear tooth surface wear
- Load misalignment
- Stator eccentricity
- Other critical machine failures
In conclusion, machine condition monitoring lets companies use real-time data from their assets to track and improve the performance and maintenance of their machines. Through this approach, companies can ensure that their machinery won't break unexpectedly and need excessive maintenance.
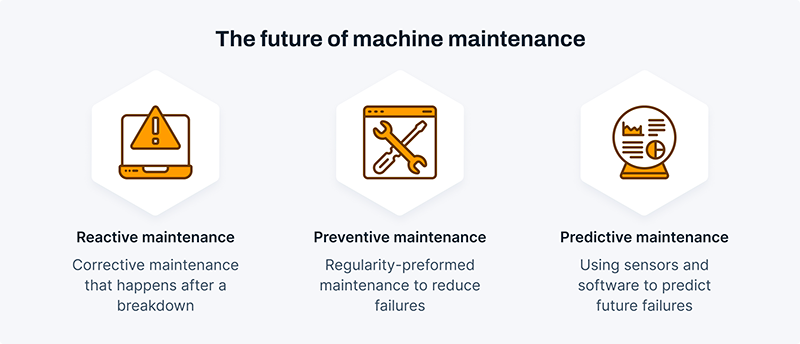
Adding condition monitoring is a key part of creating a strong, condition-based maintenance strategy or a predictive maintenance approach for industrial machinery and equipment. Therefore, manufacturers can support maintenance tasks for equipment at the right time, instead of maintaining it too much or waiting for it to break down.
Traditional machine monitoring vs. condition-based monitoring
Most manufacturing companies, on the other hand, continue to use traditional strategies like reactive or calendar-based maintenance. The primary barrier to machine condition monitoring adoption is the need for more machine condition data, which limits manufacturers' options. They can maintain equipment on a schedule or wait for failures. These ineffective solutions lead to significant waste, such as needless maintenance costs and extended periods of machine downtime.
Of course, traditional machine monitoring offers valuable machine-uptime data for quick reactions to downtime events. Condition-based monitoring, on the other hand, gives you more in-depth machine analytics. The limitations of the traditional approach impede the ability to diagnose problems accurately and adjust processes to optimize asset performance. The consequence is a reliance on either costly preventative measures or reactive maintenance, lacking a true understanding of the underlying issues.
Also, simple tracking for machine downtime forces manufacturers to either do expensive, pointless preventative maintenance or rely on reactive maintenance, which fixes the problem without really understanding what caused it until it happens again. The interesting thing is that over-maintenance, which usually happens because of a strategy based on a calendar, can be just as wasteful as unplanned downtime because it costs money and takes time.
How does machine condition monitoring work?
Condition monitoring has evolved significantly from the days of manually feeling vibrations with a wooden stick. Digital technology and the Internet have propelled it forward. Today, real-time monitoring enables engineers to schedule maintenance precisely when needed.
Modern machine condition monitoring operates in three key stages.
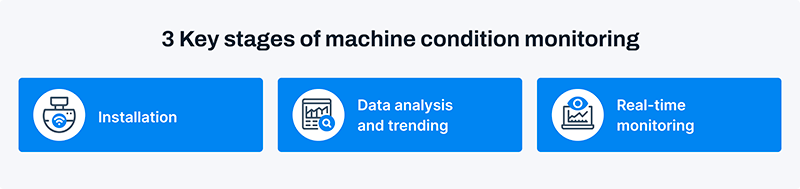
-
1Installation
The first step is the installation of IoT monitoring sensors on operational assets, including rotating machinery (turbines, compressors, pumps, motors, fans) and stationary assets (boilers, heat exchangers). Sensors are strategically placed on your equipment, capturing data measurements for vibration, temperature, and other metrics. -
2Data analysis and trending
The installation of the monitoring system allows you to start measuring the performance of your machinery. Prior to anything else, you need to take some baseline measurements. Once you have this, you can use it as a benchmark to ensure that your equipment is running at peak efficiency. -
3Real-time monitoring
The system continuously analyzes data, triggering alerts when abnormalities indicate potential issues.
The system can now monitor your systems using sensors and condition monitoring software that will evaluate performance and provide diagnostics. The system can also send out an alert when an operational abnormality is detected and assess the data to determine if immediate action is required or if the machine can operate for a while longer while maintenance is scheduled. This allows for targeted maintenance before breakdowns occur.
Why is machine condition monitoring efficient?
The global machine condition monitoring market is expected to reach $4.7 billion by 2029, growing at a compound annual growth rate of 8.3% from 2024, according to the MarketsandMarkets study. The main driver behind machine condition monitoring adoption is a rising inclination towards wireless communication.
The advent of wireless communication technology allows the deployment of small, easy-to-install sensors in areas where fixed cabling is impractical. This innovation enables high-frequency condition monitoring data acquisition, overcoming challenges related to location, cable length, and installation space availability, ultimately facilitating remote machinery monitoring.
For many industries, machine breakdowns are a costly reality. Unwanted pauses cause a halt in production, revenue losses, and may even lead to safety risks. Yet, these hurdles can be addressed with machine condition monitoring.
Condition monitoring is more than just checking if the machine is 'ON' or 'OFF'. It enables proactive maintenance. The sensors linked to your gear gather machine health data in real-time. You can tell how well your machinery works by measuring relevant indicators like temperature, vibration, and performance.
Machine condition management isn't just about fancy technology. It's about empowering informed decision-making. Operators, managers, and maintenance teams gain deeper insights into machine performance, making better choices that enhance overall production and profitability.
Think of machine condition management as the happy medium between outdated calendar-based schedules and reactive panic mode. It's mature, data-driven maintenance that extracts the most value from your equipment, ensuring a healthier, more efficient, and ultimately more prosperous operation.
As we've seen, condition-based monitoring isn't all about high-tech devices. It's about bringing actual gains to your operations. The specific benefits you can get from this proactive approach are worth going over in more detail.
Benefits of machine monitoring
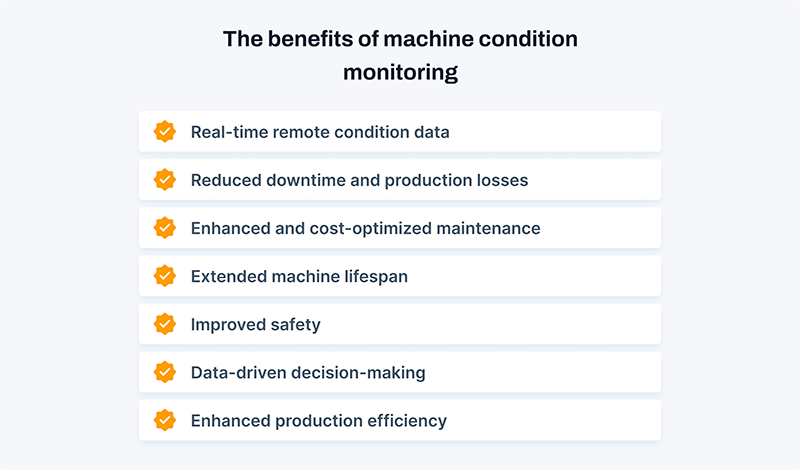
Real-time remote condition data
Machine condition monitoring isn't just about a single snapshot of equipment health. The true power lies in seeing the bigger story. It's a continuous dialogue, revealing your machinery's inner workings through real-time data streams. Tracking multiple conditions simultaneously across diverse machines unlocks data-driven insights on overall machinery health and performance.
IoT analytics can display this data in real time with push notifications, allowing engineers and operators to visualize previously invisible aspects of the condition on the shop floor. In addition, the true worth of a machine monitoring program is realized when multiple conditions can be monitored at once.
By giving a comprehensive picture of asset health over time, the collected data helps you identify the source of issues and avoid needless failures. Having this supplementary information will allow engineers to make well-informed decisions regarding their machinery and any necessary maintenance. It will also empower you to swiftly adapt to real-world conditions and plan maintenance strategically.
When a change in running levels is detected across the production chain, operators can assess the source of the problem and take appropriate action. In addition to setting health and performance thresholds, you can adjust them according to how machines are used in your operations. This allows you to plan maintenance schedules accordingly.
Your machines might not require maintenance as often as recommended. Alternatively, consider a scenario in a hot, humid facility where machines degrade faster, demanding more frequent maintenance. Condition monitoring empowers you to align schedules with actual performance, optimizing uptime and minimizing unnecessary costs.
Reduced downtime and production losses
Machine condition monitoring involves the continuous or periodic assessment of the health and performance of industrial machinery. By using various sensors and data analysis techniques, it can detect potential issues, abnormalities, or signs of wear and tear at an early stage. This early detection is critical because it allows maintenance teams to address problems before they escalate into major failures.
With the data collected through condition monitoring, predictive maintenance strategies can be implemented. Rather than following a fixed schedule for maintenance, which may lead to unnecessary downtime and production interruptions, machine condition monitoring allows maintenance activities to be scheduled based on the actual condition of the equipment. This proactive approach ensures that maintenance is performed when needed, reducing unexpected breakdowns.
By addressing potential issues before they lead to equipment failure, machine condition monitoring helps minimize unplanned downtime. Unexpected breakdowns can be disruptive to production schedules and can result in significant financial losses. By preventing these breakdowns, businesses can maintain a more consistent and reliable production flow.
Continuous monitoring allows for the optimization of equipment performance. By identifying and addressing inefficiencies or malfunctions promptly, the machinery can operate at its optimal level. This optimization contributes to maintaining a steady and reliable production process, reducing the likelihood of interruptions that can result in production losses.
Machine condition monitoring positively impacts overall equipment effectiveness (OEE), which is a metric that assesses how well equipment is utilized in terms of availability, performance, and quality. By improving the reliability and efficiency of machines, you increase OEE, which leads to higher productivity and reduced losses.
Ultimately, the reduction in downtime and production losses translates into significant cost savings for the business. Investing in machine condition monitoring technologies and practices not only enhances operational efficiency but also leads to substantial savings. It serves as a compelling justification for businesses to embrace condition-based monitoring.
Enhanced and cost-optimized maintenance
Maintenance costs, seemingly modest per asset, accumulate significantly across numerous plant-wide assets. Just a 10% reduction through condition monitoring will significantly impact overall plant profitability. This strategic planning tool enhances insight into asset management, enabling proactive maintenance before functional failures.
Opting for a 'fix as it breaks' approach may seem cost-effective initially, but it proves more expensive in the long run. Condition monitoring enhances maintenance efficiency by pinpointing faults, eliminating the need for engineers to inspect operational components while identifying issues. This not only accelerates maintenance but also cuts expenses associated with paying engineers for unproductive time, presenting a dual benefit of time and cost savings.
Extended machine lifespan
Condition monitoring not only detects anomalies but also significantly extends the lifespan of machinery. Continuous monitoring of parameters, especially those with the potential to cause severe damage, allows for preemptive assessment and repair. By addressing issues before they escalate into downtime events or cause long-term, costly damage, condition monitoring acts as a proactive safeguard for equipment longevity.
Condition-based monitoring approach not only prevents catastrophic failures but also ensures optimal performance over an extended period. Ultimately, the investment in condition monitoring translates into a prolonged equipment lifespan, contributing to overall operational efficiency and cost-effectiveness.
Improved safety
Ensuring workplace safety is paramount, especially in highly automated factories. Depending solely on handheld devices for machine health monitoring exposes workers to avoidable risks. Periodic breakdowns due to maintenance lapses further heighten employee vulnerability to hazardous conditions and potential environmental disasters.
Implementing condition monitoring is a proactive strategy. By anticipating and addressing issues before they lead to failure, it safeguards employee safety and promotes secure work practices. Owners can plan maintenance interventions in advance, minimizing risks to employees working in proximity to the machinery.
In essence, improved safety through condition monitoring not only protects the workforce but also fosters a secure and sustainable operational environment.
Data-driven decision-making
Condition monitoring boosts decision-making based on data from your machinery. You can easily access a constantly updated data repository on machinery performance and health. This wealth of information proves invaluable for formulating and analyzing key performance indicators and making informed choices based on current and historical data. It also helps optimize operating parameters and allocate resources effectively to ensure machines consistently operate at peak performance levels.
Condition-based approach empowers you to optimize operating parameters and maximize efficiency and output while minimizing wear and tear. Also, you can track key performance indicators with granularity, pinpointing areas for improvement and monitoring the impact of adjustments.
Enhanced production efficiency
Condition monitoring can also improve production efficiency by pinpointing areas for improvement. Keeping track of which parts are running poorly allows you to focus efficiency improvement efforts on those specific parts. Thus, you can improve the overall capabilities of your equipment.
Condition monitoring can also help leaders make important decisions, which improves overall production efficiency. Using condition monitoring data as a guide, this strategic approach reduces downtime and increases machinery lifetime value. Thus, you get a balance between efficient resource utilization and sustained product quality.
Machine condition monitoring solution by SIA Connect & Kaa IoT platform
Unplanned downtime due to equipment failure can cripple operations, leading to lost revenue and expensive repairs. SIA Connect and the Kaa IoT platform join forces to deliver a powerful solution that tackles this challenge head-on – a real-time machine condition monitoring system designed to keep your critical equipment running smoothly.
The integrated system seamlessly connects sensors like accelerometers to the SIA Connect gateway, capturing continuous vibration data and other relevant parameters in real-time. This data then seamlessly flows to the secure Kaa Cloud, your centralized hub for comprehensive insights on machinery health and performance. On the Kaa dashboard, operators can define routines for detecting anomalies and get notified.
The condition monitoring solution provides a real-time frequency monitoring system for critical machinery to perform maintenance at the right time and prevent unexpected downtime and machine breakages.
Let's take a look at the use case that will benefit from the machine condition monitoring solution by Kaa and SIA Connect. Consider the critical components of an offshore wind turbine: the generator, transmission, and main bearings. Real-time surveillance of their temperature and vibration can be a game-changer. A slight shift in vibration frequency might indicate shaft misalignment, while a temperature rise in a bearing could signal inadequate lubrication.
If these anomalies are not corrected in time, they can have fatal consequences. A shaft misalignment can cause severe damage to the nacelle of a wind turbine, and if the turbine is located offshore, the time and cost related to the failure are significant.
Benefits of the solution
- Cost efficient edge-to-cloud solution
The integrated solution serves as a cost-efficient edge-to-cloud system, effectively utilizing resources while providing comprehensive monitoring capabilities. By optimizing the data transmission process from edge devices to the cloud through the Kaa IoT Platform, operational costs are minimized without compromising on the breadth of monitoring. - Flexibility to add multiple sensors and communication protocols
An inherent strength of the solution lies in its flexibility to accommodate multiple sensors and communication protocols. This adaptability ensures that the monitoring system can be tailored to suit diverse industrial environments and specific machinery requirements. It allows organizations to seamlessly incorporate the latest sensor technologies and communication methods. - Simplicity in configuring sensor setup as well as notification rules
The user-friendly nature of the solution is highlighted by its simplicity in configuring sensor setups and notification rules. This ease of configuration is crucial for operators and maintenance personnel, enabling them to efficiently set up the monitoring system without the need for extensive training. The intuitive interface streamlines the process, enhancing overall usability. - Scalability in the verticals (number of sensors) and the horizontals (number of sites)
Scalability is a key feature that sets the solution apart. It can scale vertically by accommodating varying numbers of sensors, ensuring that organizations can expand or adjust their monitoring infrastructure based on the evolving needs of their machinery. Furthermore, the solution is horizontally scalable, supporting integration across multiple sites. This flexibility allows seamless deployment across diverse industrial landscapes.
Final words
In conclusion, machine condition monitoring is a powerful tool for optimizing your industrial operations. It transcends outdated calendar-based schedules and reactive panic mode, replacing them with informed, data-driven maintenance.
The benefits of machine condition monitoring are undeniable, but implementing it can be daunting. This is where SIA Connect and the Kaa IoT platform come in, offering a seamless, cost-effective solution that makes condition-based monitoring accessible to manufacturers. The given solution provides a real-time frequency monitoring system that prevents costly downtime and breakages.
With KaaIoT and SIA Connect, you can:
- Monitor critical equipment in real-time
- Identify potential issues early
- Schedule maintenance proactively
- Prevent costly breakdowns
- Improve your bottom line
Ready to unlock the power of machine condition monitoring and take your operations to the next level? Get in touch with us to learn more about how KaaIoT can help with your IIoT endeavors.